§ 18.
Обработка металла давлением
Для получения из слитка металла какого-либо изделия необходимо этот слиток обработать таким образом, чтобы получить заготовку, пригодную для изготовления изделия с минимально возможной механической обработкой. Одним из способов получения такой заготовки является обработка металлов давлением. Последняя основана на деформации, т. е. на изменении в силу пластических свойств металлов первоначальной формы и размеров исходной заготовки под воздействием внешних сил. Из металлов наибольшей пластичностью обладает свинед. Он легко деформируется при комнатной температуре. Олово, алюминий, медь и железо могут быть обработаны давлением с нагревом и без нагрева. Сталь и многие другие металлы и сплавы обрабатываются давлением только при нагреве до определенных температур. Некоторые металлы и сплавы, например марганец, чугун, и при нагреве не приобретают пластичности; такие металлы не могут обрабатываться давлением.
При пластической деформации изменяется не только форма,
но в зависимости от условий деформации (температуры, скорости и степени деформации) также структура, механические и физические свойства металла..
Основными процессами обработки металлов давлением являются: прокатка, волочение, прессование, свободная ковка, горячая и холодная штамповка.
Прокатка. Сущность прокатки заключается,в том, что металл
пропускают в зазор между двумя вращающимися в разные стороны валками на
специальных машинах —- прокатных станах. Валки обжимают заготовку, а
трение, возникающее между валками и прокатываемым материалом,
осуществляет подачу ее (рис. 6). В процессе прокатки уменьшается толщина
заготовки с одновременным увеличением длины ее. Валки для прокатки
бывают гладкими для получения металлов в виде листов.
полос и лент и калиброванными для получения
сортового и фасонного проката. Профиль, составляемый смежными ручьями
двух валков, называется калибром.
При помощи калиброванных валков получают металл различных профилей (рис.
7). Горячекатаный металл часто подвергают последующей прокатке без
нагрева — холодной прокатке. Холодная прокатка улучшает качество
поверхности, повышает точность размеров и дает возможность получить
листы, которые нельзя получить горячей прокаткой. Прокатку металла
производят на прокатных станах различных конструкций и мощности (рис.
8).
Рис. 7. Сортовые и фасонные профили проката:
1 — круглый, 2 — квадратный, 3 — полосовой, 4 — угловой, 5 — тавровый, 6
— рельсовый, 7 — двутавровый, 8 — зетовый, 9 — корытный
Рис. 8. Прокатный стан:
1 — верхний прокатный валок, 2 — указатель высоты подъема верхнего
валка, 3 — нажимной механизм, 4 — манипулятор, 5 — рольганг, 6 —
заготовка
Существует три основных способа прокатки:
продольная, косая и поперечная. Продольной прокаткой производят около
90% всего проката, в том числе весь листовой и профильный прокат.
Прессование — технологический процесс, применяемый для получения
изделий сложного поперечного сечения из пластичных цветных металлов и их
сплавов, а также из стали.
Сущность процесса прессования заключается в том, что металл, помещенный
в замкнутый объем — контейнер, подвергается высокому давлению и
выдавливается сквозь отверстие, принимая его форму.
Различают два метода прессования — прямой и обратный. При прямом
прессовании прутков (рис. 9) заготовка 1, нагретая до определенной
температуры, помещается в контейнер 2 пресса. С одной стороны контейнера
закреплена матрица 5 при помощи матрицедержателя 6. С другой стороны на
заготовку да-вит пресс-шайба 4, связанная со шплинтоном 3. Шплинт
получает необходимое давление от плунжера пресса. Под действием этого
давления металл выдавливается через отверстие матрицы. В конце процесса
прессования в контейнере остается часть металла — пресс-остаток, идущий
в отход. При обратном прессовании прутков (рис. 10) в контейнер 2 входит
не пресс-шайба, а полый пуансон 3 с матрицей 4 на конце. Матрица давит
на
заготовку 1, и металл течет в отверстие матрицы
навстречу движению пуансона. При обратном методе снижаются отходы
металла на прессостаток и уменьшается усилие деформации, но усложняется
конструкция пресса.
Прямое прессование труб (рис. 11) отличается от предыдущих методов
наличием иглы 2, которая проходит через отверстие в заготовке 1. Длина
иглы несколько превышает высоту заго-
товки. При давлении пресс-шайбы 3 на заготовку
металл выдавливается в зазор между матрицей 4 и иглой 2, образуя трубу
5. Внутренний диаметр трубы равен диаметру иглы, наружный — диаметру
отверстия в матрице.
Прессование выполняют на гидравлических прессах вертикального и
горизонтального типов большой мощности.
Холодное волочение. Прокаткой можно получить только сравнительно
толстую проволоку с большими допусками по размерам. Тонкую проволоку,
точную по размерам, получают последовательным протаскиванием
горячекатаной проволоки (подката) через фильер на специальных
волочильных станах. Подкат перед волочением отжигают и подвергают
травлению
в растворе серной кислоты с последующей
нейтрализацией. После этого заходный конец проволоки обжимают на
специальных валках, протаскивают через фильер и захватывают клещами
барабана, который вращаясь, тянет проволоку через фильер и обжимает ее
на меньший диаметр. Обжатие выбирается такое, чтобы усилие волочения
было меньше разрывающего проволоку.
Для изготовления деталей на автоматах требуется штанговый металл точных
размеров. Такой металл получают волочением. Принцип волочения штангового
металла тот же, что и волочения проволоки (рис. 12). После волочения
штанговый металл необходимо править. Правку осуществляют на
роликоправильных станах различной конструкции и на прессах.
Свободная ковка разделяется на ручную и
машинную. Ручной ковкой можно изготовлять только мелкие поковки. Такую
ковку применяют в небольших ремонтных мастерских. Основным видом
свободной ковки в машиностроении является машинная ковка. Операциями
ковки являются осадка, вытяжка, прошивка, рубка, гибка, закручивание и
кузнечная сварка. Осадкой (рис. 13) уменьшают высоту заготовки и
увеличивают ее поперечное сечение; частный случай осадки — высадка.
Вытяжка производится между бойками молота (рис. 14), причем заготовку
кладут поперек бойков, передвигая и кантуя ее после каждого удара.
Прошивание отверстий производят с помощью прошивня. Прошиваемую
заготовку кладут на нижний боек и ударами верхнего бойка вбивают
прошивень приблизительно до половины толщины заготовки (рис. 15); при
этом металл из-под прошивня течет в стороны и заготовка изгибается
кверху. Затем заготовку поворачивают и вбивают прошивень с другой
стороны (рис. 16). В конце операции прошивнем срезают часть металла в
виде диска. Расширяют и выравнивают отверстия с помощью бочкообразных
оправок (рис. 17). Рубкой заготовку разделяют на части (рис. 18). При
гибке заготовке придают изогнутую форму (рис. 19, а). При закручивании
одну часть заготовки поворачивают относительно другой части заготовки
под определенным углом вокруг общей оси (рис. 19,б). Машинной ковкой
можно
изготовить поковки массой до 200 т и более. Машинную ковку производят на молотах и прессах различной конструкции и мощности.
Горячая штамповка является одним из распространенных видов
обработки металла давлением. При горячей штамповке для придания
заготовке требуемой формы пользуются
штампом, имеющим полость, конфигурация которой соответствует форме изготовляемой детали. Горячая штамповка по сравнению со свободной ковкой имеет 'следующие преимущества: высокую производительность, однородность и точность получаемых поковок.
Горячую штамповку применяют для массового и
крупносерийного производства, требуя для каждого изделия отдельного
штампа, на изготовление которого затрачиваются значительное время и
денежные средства. Штамп (рис. 20) состоит из двух половин: верхней,
закрепляемой при помощи клиньев в бабе молота, или подвижной части
пресса и нижней, устанавливаемой в штамподержателе, соединенном с
шаботом молота, или неподвижной части пресса. В обеих половинах штампа
выполнены ручьи, образующие при соприкосновении этих половин полость с
очертанием, соответствующим конфигурации формы штампуемого изделия.
Для поковок сложной конфигурации применяют многоручьевые штампы (рис.
21). Штамп в работе испытывает большие ударные нагрузки, поэтому его
изготовляют из хорошо прокованной высоколегированной стали и подвергают
термической обработке. Штампы с глубокими ручьями смазывают мазутом. При
сгорании во время штамповки мазут образует газы, расширение которых при
нагреве за счет тепла поковки облегчает удаление готовой поковки из
окончательного ручья штампа. Одновременно с этим смазка штампов
уменьшает их «разгар», который образуется в виде мелких трещин от
многократного нагрева и охлаждения верхнего слоя металла штампа.
При нагреве заготовок под штамповку на них образуется окалина, которая
во время штамповки отделяется от заготовок
и попадает в полость штампов. Чтобы не заштамповать окалину в поковку, ее выд\гвают из полости штампа струей воздуха под давлением 6 ат. При штамповке в месте разъема штампов на
поковках образуются заусенцы (облой), которые
обрезаются на специальных обрезных штампах. На поковках из легированной
и высокоуглеродистой стали обрезка облоя должна производиться на горячих
поковках непосредственно после ковки. При обрезке облоя на холодных
поковках по месту разъема могут возникнуть трещины.
Нагрев заготовок под штамповку производят в угольных, нефтяных, газовых
и электрических печах. Во всех случаях стремятся нагревать заготовки без
образования окалины (без окисления поверхности).
За последнее время на ряде передовых заводов для нагрева заготовок под
штамповку применяют высокочастотные установки. Их применение ускоряет
нагрев заготовок, устраняет повы-шеннное окисление поверхности, делает
возможной автоматизацию процесса нагрева и совершенно исключает пережог.
Холодная штамповка применяется для
изготовления изделий из листовой стали, алюминия и его сплавов, меди,
латуни. сплавов магния и др. Исходным материалом для штамповки служат
ленты, листы и полосы, имеющие толщину от десятых долей до 6—8 мм.
Листовая штамповка имеет большое распространение во всех отраслях
промышленности; детали после листовой штамповки, являясь точными по
размерам, применяются почти без механической обработки.
Холодную штамповку выполняют с помощью штампов на различного рода
прессах. Конструирование штампов выполняется так, чтобы при штамповке
материал не делался тоньше.
При штамповке деталей сложной конфигурации в несколько операций
производится промежуточный отжиг. Отжиг штамповок производят в печах с
защитной атмосферой, так как наличие окалины на поверхности деталей
приводит к браку.
Процесс изготовления деталей холодной штамповкой состоит из ряда
операций, которые делятся на две группы: разделительные (отрезка,
вырубка, пробивка и зачистка) и формоизменяющие (гибка, вытяжка и
отбортовка).
Содержание
- 1. Г.В. Просяник Изготовление оболочковых форм и стержней читать онлайн
- 2. Введение - Изготовление оболочковых форм и стержней
- 3. Общие сведения о металлах и сплавах
- 4. Понятие о структуре сплавов
- 5. Понятие о коррозии металлов
- 6. Серый чугун
- 7. Ковкий чугун
- 8. Углеродистые стали для фасонных отливок
- 9. Легированные стали со специальными свойствами
- 10. Маркировка углеродистых и легированных сталей
- 11. Термическая и химико-термическая обработка сталей
- 12. Цветные металлы и сплавы
- 13. Металлокерамические твердые сплавы
- 14. Абразивные материалы
- 15. Обработка металла давлением
- 16. Сварка металлов
- 17. Обработка металлов резанием
- 18. Основные сведения о слесарной обработке
- 19. Схема технологического процесса производства отливок
- 20. Понятие о свойствах формовочных и стержневых смесей
- 21. Песчано-глинистые материалы
- 22. Связующие материалы в литейном производстве
- 23. Противопригарные материалы в литейном производстве
- 24. Высокоогнеупорные материалы в литейном производстве
- 25. Формовочные и стержневые смеси в литейном производстве
- 26. Контроль формовочных материалов и смесей в литейном производстве
- 27. Основные сведения о литейной оснастке
- 28. Изготовление литейных форм и стержней
- 29. Элементы литниковых систем
- 30. Основные типы плавильных печей
- 31. Заливка литейных форм
- 32. Выбивка форм, очистка и обрубка отливок
- 33. Специальные виды литья
- 34. Литье под давлением
- 35. Литье по выплавляемым моделям
- 36. МЕХАНИЗАЦИЯ И АВТОМАТИЗАЦИЯ ЛИТЕЙНОГО ПРОИЗВОДСТВА
- 37. Элементы механизации процессов приготовления и раздачи формовочных истержневых смесей
- 38. Механизация и автоматизация формовочных и стержневых работ
- 39. Основы механизации и автоматизации составления и загрузки шихты взагранку
- 40. Пути автоматизации заливки литейных форм
- 41. Механизация и автоматизация выбивки и очистки отливок
- 42. Механизация транспортных средств в литейном производстве
- 43. Синтетические смолы
- 44. Фенолформальдегидные резольные смолы
- 45. Понятие о методах испытаний связующих в литейном производстве
- 46. Характеристика катализаторов в литейном производстве
- 47. Формовочные лески в литейном производстве
- 48. Новые формовочные материалы в литейном производстве
- 49. Добавки в песчано-смоляные смеси в литейном производстве
- 50. Разделительные составы в литейном производстве
- 51. Противопригарные покрытия в литейном производстве
- 52. Клеи для оболочковых форм
- 53. Типы песчано-смоляных смесей
- 54. Методы испытания песчано-смоляных смесей
- 55. Механические свойства песчано-смоляных смесей
- 56. Механические свойства песчано-смоляных смесей - часть 2
- 57. Физико-химические свойства песчано-смоляных смесей
- 58. Технологические свойства песчано-смоляных смесей
- 59. Составы песчано-смоляных смесей
- 60. Методы изготовления оболочковых форм из сухих песчано-смоляных смесей
- 61. Свободная насыпка с помощью рамки
- 62. Методы изготовления оболочковых форм из сухих песчано-смоляных смесей -часть 3
- 63. Методы изготовления оболочковых стержней из сухих песчано-смоляных смесей
- 64. Формирование оболочковых стержней с помощью центробежного метода
- 65. Методы изготовления оболочковых форм и стержней из сырых песчано-смоляныхсмесей
- 66. Зависимость физико-механических свойств оболочковых форм и стержней отспособа изготовления
- 67. Способы скрепления оболочковых полуформ
- 68. Машины для изготовления сухих песчано-смоляных смесей
- 69. Машины для изготовления сырых песчано-смоляных смесей
- 70. Основные правила техники безопасности при работе на оборудовании дляизготовления песчано-смоляных смесей
- 71. Элементы установок для изготовления оболочковых форм и стержней из сухойсмеси
- 72. Элементы установок для изготовления оболочковых форм и стержней из сухойсмеси - часть 2
- 73. Элементы установок для изготовления оболочковых форм и стержней из сыройпесчано-смоляной смеси
- 74. Машины для изготовления оболочковых форм из сухой смеси
- 75. автоматические машины АКФ-2
- 76. четырехпозиционная карусельная машина модели 2Б31
- 77. Установка МДФ-240
- 78. Шестипозиционная пескострельно-прессовая установка для изготовлениястопочных оболочковых форм
- 79. Машины для изготовления оболочковых стержней из сухих смесей
- 80. Машина для механизации процесса изготовления оболочковых стержнейнасыпным способом
- 81. установки модели 91875
- 82. Стержневая пескодувная машина конструкции Минского филиала НИИАвтопром
- 83. автомат марки АЦИС-10
- 84. Машины для изготовления оболочковых форм и стержней из сыройпесчано-смоляной смеси
- 85. Установка модели 2БН83 для изготовления оболочковых стержней из сырыхсмесей
- 86. Установка модели 4509Б для изготовления стержней коробчатой конструкцииили оболочковых форм из сырой смеси
- 87. Приспособление для механического скрепления оболочковых полуформ
- 88. Оборудование для скрепления оболочковых полуформ - часть 2
- 89. Полуавтоматическая установка модели 40П-4502
- 90. Установка модели 880 для склеивания оболочковых полуформ
- 91. Высокочастотная установка для склеивания оболочковых полуформ
- 92. Установка карусельного типа для склеивания оболочковых полу-форм
- 93. Основные правила техники безопасности при работе на оборудовании дляизготовления оболочковых форм и стержней
- 94. МОДЕЛЬНАЯ ОСНАСТКА ДЛЯ ИЗГОТОВЛЕНИЯ ОБОЛОЧКОВЫХ ФОРМ И СТЕРЖНЕЙ
- 95. Модельные плиты в литейном производстве
- 96. Элементы литниковых систем
- 97. Вспомогательные устройства при литье в оболочковые формы и стержни
- 98. Приспособления для съема оболочек с плиты в литейном производстве
- 99. Стержневые ящики для изготовления оболочковых стержней
- 100. Заливка форм для получения отливок
- 101. Выбивка отливок из оболочковых форм
- 102. Очистка отливок, полученных в оболочковых формах
- 103. Растрескивание оболочковых форм в литейном производстве
- 104. Рыхлоты и неоднородность поверхности оболочки и стержня
- 105. Коробление оболочковых форм
- 106. Газовые раковины в отливках
- 107. Неметаллические включения в отливках
- 108. Неслитины и спаи в отливах
- 109. Усадочные раковины в отливках
- 110. Литература (Изготовление оболочковых форм и стержней)
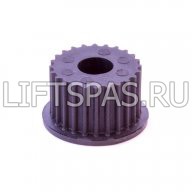
от 910.00 руб./шт.
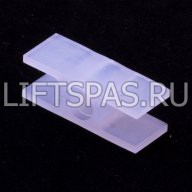
от 0.00 руб./шт.
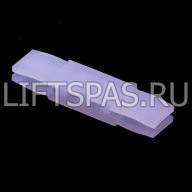
от 0.00 руб./шт.
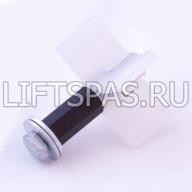
от 1500.00 руб./шт.
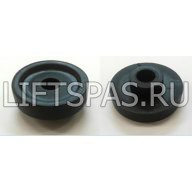
от 109.00 руб./шт.
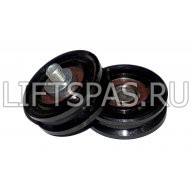
от 167.00 руб./шт.
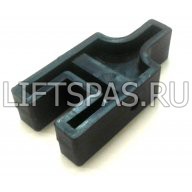
от 46.00 руб./шт.
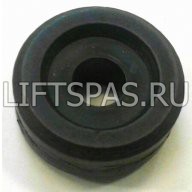
от 109.00 руб./шт.
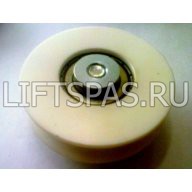
от 1426.00 руб./шт.
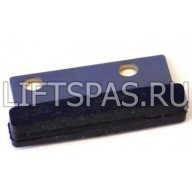
от 0.00 руб./шт.
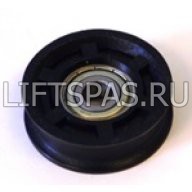
от 334.00 руб./шт.
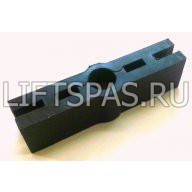
от 265.00 руб./шт.