§ 12.
Термическая и химико-термическая обработка сталей
Термическая (тепловая) обработка стали служит для изменения в определенных пределах прочности, твердости, вязкости, упругости, износостойкости и других свойств стального изделия. Большинство термических процессов не меняет химического состава стали. Исключением являются процессы химико-термической обработки, которые изменяют химический состав поверхностных слоев.
Целью химико-термической обработки является получение поверхностного слоя стальных деталей, обладающих повышенной твердостью, износоустойчивостью, жаростойкостью или коррозионной стойкостью. Для этого нагретые детали подвергают воздействию среды, из которой путем диффузии (проникновения) в поверхностный слой деталей переходят некоторые элементы (углерод, азот, алюминий, хром, кремний и др.). Выделяющийся при разложении активизированный атом элемента проникает в решетку кристаллов стали и образует твердый раствор или химическое соединение. Наиболее распространенными видами химико-термической обработки стали являются: цементация (насыщение поверхности углеродом), цианирование жидкое и газовое (насыщение поверхности азотом и углеродом), алитирование (насыщение поверхности алюминием), силици-рование (насыщение поверхности кремнием), борнрование (насыщение поверхности бором) и др.
Способами термической обработки без изменения химического состава металла являются нормализация, отжиг, закалка и отпуск.
Нормализация применяется для того, чтобы перевести структуру стали в однородное состояние, ликвидировать крупнозернистую структуру, которую имеет сталь в литом или кованном состоянии. Нормализация заключается в нагреве до температуры, при которой углерод полностью растворяется в железе, и охлаждении на воздухе. Нормализованная сталь имеет более высокие, чем в литом состоянии, показатели по вязкости и более низкую твердость, что создает хорошие условия для обработки резанием. Нормализацию применяют для выравнивания внутренних напряжений в отливках, поковках и сварных соединениях.
Отжигом называют процесс, при котором производят нагрев выше температуры полного растворения углерода в железе, выдержку при этой температуре и затем медленное охлаждение до комнатной температуры. Отжиг применяют для улучшения обрабатываемости резанием и для повышения пластичности и вязкости.
Закалкой называют процесс термической обработки, состоящий из нагрева выше точки полного растворения углерода в железе, выдержки при этой температуре в течение определенного времени и последующего быстрого охлаждения (в воде, в
масле и других средах). Скорость нагрева,
длительность выдержки и охлаждающая среда при закалке применяются в
зависимости от химического состава стали, величины и массы изделия, типа
печи и т. д. Для получения детали с вязкой сердцевиной и твердой рабочей
поверхностью применяют поверхностную закалку.
Отпуск состоит из нагрева закаленной стали ниже температуры начала
растворения углерода в железе, выдержки и последующего быстрого или
медленного охлаждения. Выбор температуры отпуска зависит от назначения
изделий. Скорость охлаждения после отпуска для простой углеродистой
стали не имеет значения, но специальные стали, например хромоникелевые,
во избежание получения низких механических свойств (особенно ударной
вязкости) необходимо охлаждать быстро.
Обработка холодом. При недостаточном отпуске закаленного режущего
инструмента получают пониженную твердость, что резко снижает его
работоспособность. Для повышения твердости инструмент подвергают
обработке холодом при температурах ниже нуля (от —40 до —120°С). Такие
охлаждающие температуры создают при помощи жидкого кислорода и воздуха,
смеси сухого льда (твердый С02) с ацетоном, спиртом, жидкого азота и т.
д.
После выдержки в этой среде в течение определенного времени твердость
инструмента повышается. Повышение твердости вызывается изменением
структурного состояния материала инструмента и сопровождается
возникновением внутренних напряжений. Поэтому после обработки холодом
необходимо производить отпуск при температурах, не понижающих твердость,
но достаточных для снятия внутренних напряжений (например, для
цементируемых деталей температура отпуска лежит в пределах от +160 до
+180° С).
Обработку холодом применяют также для стабилизации размеров и формы
измерительных инструментов.
Цементация. Сущность процесса цементации состоит в том, что при
нагревании низкоуглеродистой стали в среде, способной отдавать углерод,
поверхностный слой стали поглощает углерод и изменяет свой химический
состав. После соответствующей термической обработки цементированные
изделия приобретают высокую твердость поверхности, сохраняя вязкую
сердцевину. Цементацию широко применяют при изготовлении деталей,
подвергающихся истиранию и одновременно испытывающих ударную нагрузку. В
зависимости от среды, отдающей углерод, цементация бывает твердая,
жидкостная и газовая. При цементации в твердом карбюризаторе средой
являются смеси, в состав которых входят древесный уголь, кокс,
обугленная кожа, смешанные с углекислым барием или другими углекислыми
солями.
При газовой цементации активным науглероживающим элементом среды
является метан СН4. Для газовой цементации де-талями заполняют плотные
муфели, через которые пропускают газ. В муфелях поддерживают температуру
в пределах 900— 950° С.
Цианирование — насыщение поверхностного слоя изделия одновременно
углеродом и азотом. Цианирование применяют для повышения поверхностной
твердости и плоскостности.
Жидкостное цианирование производят в ваннах с расплавами цианистых солей
(NaCN, KCN, Ca(CN)2 и др.) при температуре, достаточной для разложения
их с выделением активных атомов углерода и азота.
Газовое цианирование отличается от газовой цементации тем, что к
цементирующему газу добавляют аммиак, дающий активизированные атомы
азота,
Алитирование представляет собой поверхностное насыщение деталей
алюминием с образованием твердого раствора алюминия в железе. Оно
применяется преимущественно к деталям, работающим при высоких
температурах (колосники, трубы и др.), так как значительно повышает
стойкость стали при высокой температуре (1000°С).
Диффузное хромирование производится в порошковых смесях, состоящих из
феррохрома и шамота, смоченных соляной кислотой, или в газовой среде при
разложении паров хлорида хрома (СгС12). Хромированный слой
низкоуглеродистой стали незначительно повышает твердость, но обладает
большой вязкостью, что позволяет подвергать хромированные детали
сплющиванию, прокатке и т. п.
Силицирование — насыщение поверхностного слоя стальных изделий кремнием,
обеспечивающее повышение стойкости против коррозии и эрозии в морской
воде, азотной, серной и соляной кислотах.
Содержание
- 1. Г.В. Просяник Изготовление оболочковых форм и стержней читать онлайн
- 2. Введение - Изготовление оболочковых форм и стержней
- 3. Общие сведения о металлах и сплавах
- 4. Понятие о структуре сплавов
- 5. Понятие о коррозии металлов
- 6. Серый чугун
- 7. Ковкий чугун
- 8. Углеродистые стали для фасонных отливок
- 9. Легированные стали со специальными свойствами
- 10. Маркировка углеродистых и легированных сталей
- 11. Термическая и химико-термическая обработка сталей
- 12. Цветные металлы и сплавы
- 13. Металлокерамические твердые сплавы
- 14. Абразивные материалы
- 15. Обработка металла давлением
- 16. Сварка металлов
- 17. Обработка металлов резанием
- 18. Основные сведения о слесарной обработке
- 19. Схема технологического процесса производства отливок
- 20. Понятие о свойствах формовочных и стержневых смесей
- 21. Песчано-глинистые материалы
- 22. Связующие материалы в литейном производстве
- 23. Противопригарные материалы в литейном производстве
- 24. Высокоогнеупорные материалы в литейном производстве
- 25. Формовочные и стержневые смеси в литейном производстве
- 26. Контроль формовочных материалов и смесей в литейном производстве
- 27. Основные сведения о литейной оснастке
- 28. Изготовление литейных форм и стержней
- 29. Элементы литниковых систем
- 30. Основные типы плавильных печей
- 31. Заливка литейных форм
- 32. Выбивка форм, очистка и обрубка отливок
- 33. Специальные виды литья
- 34. Литье под давлением
- 35. Литье по выплавляемым моделям
- 36. МЕХАНИЗАЦИЯ И АВТОМАТИЗАЦИЯ ЛИТЕЙНОГО ПРОИЗВОДСТВА
- 37. Элементы механизации процессов приготовления и раздачи формовочных истержневых смесей
- 38. Механизация и автоматизация формовочных и стержневых работ
- 39. Основы механизации и автоматизации составления и загрузки шихты взагранку
- 40. Пути автоматизации заливки литейных форм
- 41. Механизация и автоматизация выбивки и очистки отливок
- 42. Механизация транспортных средств в литейном производстве
- 43. Синтетические смолы
- 44. Фенолформальдегидные резольные смолы
- 45. Понятие о методах испытаний связующих в литейном производстве
- 46. Характеристика катализаторов в литейном производстве
- 47. Формовочные лески в литейном производстве
- 48. Новые формовочные материалы в литейном производстве
- 49. Добавки в песчано-смоляные смеси в литейном производстве
- 50. Разделительные составы в литейном производстве
- 51. Противопригарные покрытия в литейном производстве
- 52. Клеи для оболочковых форм
- 53. Типы песчано-смоляных смесей
- 54. Методы испытания песчано-смоляных смесей
- 55. Механические свойства песчано-смоляных смесей
- 56. Механические свойства песчано-смоляных смесей - часть 2
- 57. Физико-химические свойства песчано-смоляных смесей
- 58. Технологические свойства песчано-смоляных смесей
- 59. Составы песчано-смоляных смесей
- 60. Методы изготовления оболочковых форм из сухих песчано-смоляных смесей
- 61. Свободная насыпка с помощью рамки
- 62. Методы изготовления оболочковых форм из сухих песчано-смоляных смесей -часть 3
- 63. Методы изготовления оболочковых стержней из сухих песчано-смоляных смесей
- 64. Формирование оболочковых стержней с помощью центробежного метода
- 65. Методы изготовления оболочковых форм и стержней из сырых песчано-смоляныхсмесей
- 66. Зависимость физико-механических свойств оболочковых форм и стержней отспособа изготовления
- 67. Способы скрепления оболочковых полуформ
- 68. Машины для изготовления сухих песчано-смоляных смесей
- 69. Машины для изготовления сырых песчано-смоляных смесей
- 70. Основные правила техники безопасности при работе на оборудовании дляизготовления песчано-смоляных смесей
- 71. Элементы установок для изготовления оболочковых форм и стержней из сухойсмеси
- 72. Элементы установок для изготовления оболочковых форм и стержней из сухойсмеси - часть 2
- 73. Элементы установок для изготовления оболочковых форм и стержней из сыройпесчано-смоляной смеси
- 74. Машины для изготовления оболочковых форм из сухой смеси
- 75. автоматические машины АКФ-2
- 76. четырехпозиционная карусельная машина модели 2Б31
- 77. Установка МДФ-240
- 78. Шестипозиционная пескострельно-прессовая установка для изготовлениястопочных оболочковых форм
- 79. Машины для изготовления оболочковых стержней из сухих смесей
- 80. Машина для механизации процесса изготовления оболочковых стержнейнасыпным способом
- 81. установки модели 91875
- 82. Стержневая пескодувная машина конструкции Минского филиала НИИАвтопром
- 83. автомат марки АЦИС-10
- 84. Машины для изготовления оболочковых форм и стержней из сыройпесчано-смоляной смеси
- 85. Установка модели 2БН83 для изготовления оболочковых стержней из сырыхсмесей
- 86. Установка модели 4509Б для изготовления стержней коробчатой конструкцииили оболочковых форм из сырой смеси
- 87. Приспособление для механического скрепления оболочковых полуформ
- 88. Оборудование для скрепления оболочковых полуформ - часть 2
- 89. Полуавтоматическая установка модели 40П-4502
- 90. Установка модели 880 для склеивания оболочковых полуформ
- 91. Высокочастотная установка для склеивания оболочковых полуформ
- 92. Установка карусельного типа для склеивания оболочковых полу-форм
- 93. Основные правила техники безопасности при работе на оборудовании дляизготовления оболочковых форм и стержней
- 94. МОДЕЛЬНАЯ ОСНАСТКА ДЛЯ ИЗГОТОВЛЕНИЯ ОБОЛОЧКОВЫХ ФОРМ И СТЕРЖНЕЙ
- 95. Модельные плиты в литейном производстве
- 96. Элементы литниковых систем
- 97. Вспомогательные устройства при литье в оболочковые формы и стержни
- 98. Приспособления для съема оболочек с плиты в литейном производстве
- 99. Стержневые ящики для изготовления оболочковых стержней
- 100. Заливка форм для получения отливок
- 101. Выбивка отливок из оболочковых форм
- 102. Очистка отливок, полученных в оболочковых формах
- 103. Растрескивание оболочковых форм в литейном производстве
- 104. Рыхлоты и неоднородность поверхности оболочки и стержня
- 105. Коробление оболочковых форм
- 106. Газовые раковины в отливках
- 107. Неметаллические включения в отливках
- 108. Неслитины и спаи в отливах
- 109. Усадочные раковины в отливках
- 110. Литература (Изготовление оболочковых форм и стержней)
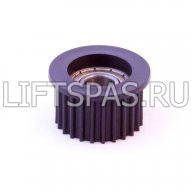
от 890.00 руб./шт.
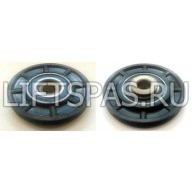
от 185.00 руб./шт.
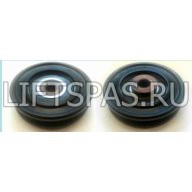
от 132.00 руб./шт.
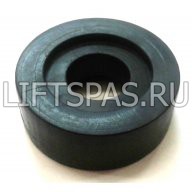
от 103.00 руб./шт.
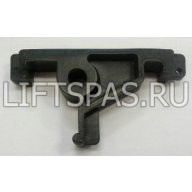
от 391.00 руб./шт.
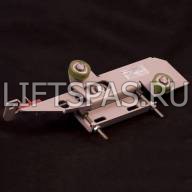
от 17 518.00 руб./шт.
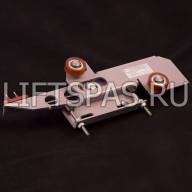
от 17 518.00 руб./шт.
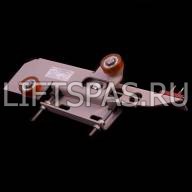
от 17 518.00 руб./шт.
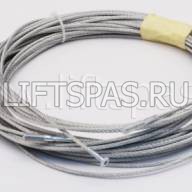
от 2559.00 руб./шт.
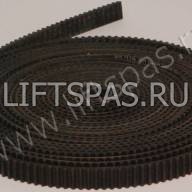
от 1578.00 руб./шт.
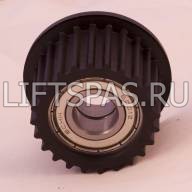
от 890.00 руб./шт.